深析國(guó)內(nèi)依賴進(jìn)口的鋰電池隔膜技術(shù)
5.兩種鋰離子電池隔膜工藝核心技術(shù)
本文引用地址:http://www.butianyuan.cn/article/201707/361882.htm對(duì)于濕法工藝來(lái)說(shuō),樹(shù)脂與添加劑的擠出混合過(guò)程以及拉伸過(guò)程是該工藝的兩大核心問(wèn)題。擠出過(guò)程要求物料混合效果好、塑化能力強(qiáng)、擠出過(guò)程穩(wěn)定,拉伸過(guò)程決定了分子鏈的取向以及制孔劑分布是否均勻。對(duì)于干法工藝來(lái)說(shuō),除了擠出混合過(guò)程外,熔融牽伸比以及熱處理都是核心過(guò)程。
目前,全球制造隔膜的廠家以濕法為主,濕法隔膜的價(jià)格較貴,未來(lái)濕法隔膜在動(dòng)力電池中仍將走高端的市場(chǎng)路線,而中低端動(dòng)力電池仍將以干法為主。
6.全球鋰離子電池隔膜企業(yè)
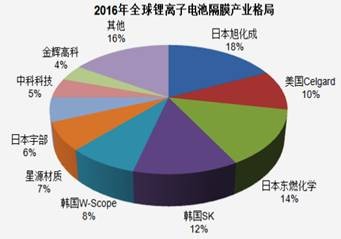
全球范圍內(nèi)的鋰離子電池隔膜的市場(chǎng)需求量呈逐年遞增的趨勢(shì),隔膜出貨量從2009年的2.4億平米增至2014年的11.85億平米。日本旭化成、日本東燃化學(xué)以及美國(guó)Celgard(Celgard于2015年2月被濕法技術(shù)代表公司旭化成收購(gòu),干法生產(chǎn)線停產(chǎn)并新建立濕法生產(chǎn)線)是隔膜三巨頭,占據(jù)的全球市場(chǎng)份額曾高達(dá)77%。但隨著韓國(guó)和中國(guó)企業(yè)的崛起,三巨頭的份額在快速下滑,2014年占比56%左右。
7.我國(guó)鋰離子電池隔膜差距
鋰電池隔膜是四大材料中技術(shù)壁壘最高的部分,其成本占比僅次于正極材料,約為10%~14%,在一些高端電池中,隔膜成本占比甚至達(dá)到20%。
我國(guó)鋰離子電池隔膜在干法工藝上已經(jīng)取得重大突破,目前已經(jīng)具備國(guó)際一流的制造水平。但在濕法隔膜領(lǐng)域,國(guó)內(nèi)隔膜企業(yè)受限于工藝、技術(shù)等多方面因素,產(chǎn)品水平還較低,生產(chǎn)設(shè)備主要依賴進(jìn)口。我國(guó)的隔膜產(chǎn)品在厚度、強(qiáng)度、孔隙率一致性方面與國(guó)外產(chǎn)品有較大差距,產(chǎn)品批次一致性也有待提高。
鋁塑膜
1.鋰離子電池鋁塑膜的作用
鋁塑膜是鋰離子電池五大材料之一,是軟包鋰電池封裝材料。鋁塑膜由外層尼龍層/粘合劑/中間層鋁箔/粘合劑/內(nèi)層熱封層,共五層組成,每層功能要求都比較高。典型的鋁塑膜結(jié)構(gòu)如下圖所示:
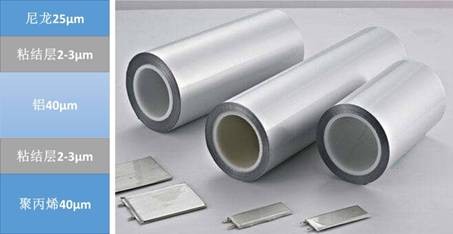
2.鋰離子電池對(duì)鋁塑膜的要求
鋁塑膜的阻隔能力、耐穿刺能力、電解液穩(wěn)定性、耐高溫性和絕緣性影響著鋰離子電池的使用性能。任何一個(gè)方面有所缺失,都有可能導(dǎo)致電池性能下降,直接報(bào)廢。鋁塑膜采用精密涂布技術(shù)生產(chǎn),目前,日本企業(yè)具有世界上最先進(jìn)的精密涂布技術(shù)。
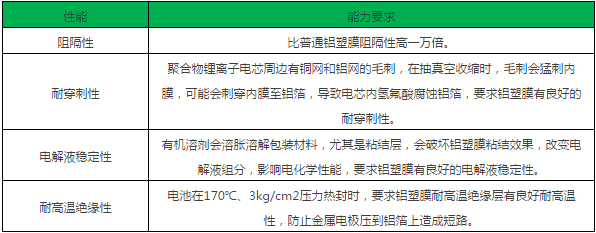
3.鋰離子電池鋁塑膜工藝
干法和熱法工藝是鋁塑膜主要采用的生產(chǎn)工藝。干法工藝是鋁和聚丙烯用粘合劑粘結(jié)后直接壓合而成,熱法工藝是鋁和聚丙烯之間用MPP接著,在緩慢升溫升壓熱壓合而成。
干法生產(chǎn)的鋁塑膜薄,外觀好,具有優(yōu)良的深沖性能和防短路性能,且工藝簡(jiǎn)單、成本低,然而與熱法相比,耐電解液和抗水性能較差;熱法的優(yōu)點(diǎn)在耐電解液和抗水性能好,但是深沖成型性能、防短路性能不如干法,外觀和裁切性差。
4.全球鋰離子電池鋁塑膜企業(yè)
在軟包鋰電池中鋁塑膜起到關(guān)鍵的作用,一般占到電芯成本的15-20%左右。然而國(guó)內(nèi)由于技術(shù)的不足,鋁塑膜市場(chǎng)占比非常少,占比不足5%。目前國(guó)內(nèi)鋁塑膜市場(chǎng)90%份額被日本廠商壟斷,主要是DNP(大日本印刷)、昭和電工和T&T占據(jù)。
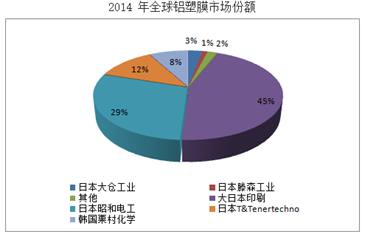
鋁塑膜作為尚未實(shí)現(xiàn)國(guó)產(chǎn)化的鋰電材料,其毛利率高達(dá)60-80%。據(jù)估計(jì),目前鋁塑膜全球市場(chǎng)空間僅為數(shù)十億元,隨著下游需求放量,行業(yè)增速有望超過(guò)40%,潛在市場(chǎng)規(guī)模將達(dá)百億級(jí)別。
5.我國(guó)鋰離子電池鋁塑膜差距
作為軟包電池的核心材料,鋁塑膜的生產(chǎn)技術(shù)難度遠(yuǎn)高于隔膜、正極、負(fù)極、電解液,是鋰電池行業(yè)內(nèi)三大高技術(shù)之一。從產(chǎn)品性能上看,我國(guó)鋁塑膜產(chǎn)品與國(guó)外產(chǎn)品存在較大差距,主要表現(xiàn)在:鋁箔表面處理工藝落后、污染大;鋁箔的水處理會(huì)產(chǎn)生“氫脆”,導(dǎo)致鋁塑膜耐拆度差;鋁箔表面挺度不夠,良品率差;聚丙烯與高導(dǎo)熱的鋁箔表面復(fù)合時(shí)易卷曲,產(chǎn)生層狀結(jié)晶;國(guó)內(nèi)膠粘劑配方工藝較差,易出現(xiàn)分層剝離問(wèn)題。
由于這些生產(chǎn)工藝技術(shù)的不足,我國(guó)生產(chǎn)的鋁塑膜產(chǎn)品沖深最大在5mm左右,始終無(wú)法達(dá)到良好的性能要求。而國(guó)外可達(dá)到8mm,有的甚至達(dá)到12mm,總體與國(guó)外產(chǎn)品還有一定差距;厚度方面,國(guó)內(nèi)鋁塑膜最薄只能做到70μm,量產(chǎn)的有112、88和72μm,而日本鋁塑膜最薄可以做到40μm,65和48μm的也實(shí)現(xiàn)量產(chǎn)。
為何鋁塑膜的制造技術(shù)難以突破,總體來(lái)說(shuō)主要是材料、設(shè)備、工藝方面存在不足,其技術(shù)難度主要在于工藝的控制—反應(yīng)條件的精確控制。
評(píng)論