刀具破損的聲發(fā)射傳感監(jiān)測(cè)新技術(shù)
L(n)=λ.max|xi(n)| (1)
式中L(n)—聲發(fā)射幅值閾值;
n—浮動(dòng)次數(shù);λ—系數(shù);
xi—聲發(fā)射包絡(luò)信號(hào)的采樣序列值(i為采樣序號(hào))。
進(jìn)入監(jiān)測(cè)狀態(tài)后,首先進(jìn)行采樣,取得工況環(huán)境噪聲信號(hào)數(shù)據(jù)xi(0),依據(jù)式(1)取采樣序列的最大值乘以系數(shù)λ作為閾值。以后自動(dòng)定期采樣,取得工況環(huán)境噪聲信號(hào)數(shù)據(jù)xi(n),重新按式(1)確定新的閾值,這樣閾值就隨工況條件變化而變化。其中系數(shù)λ由工況條件確定。例如在輕負(fù)載的條件下λ=1.50;在中等負(fù)載的條件下λ=1.30;在重負(fù)載的條件下λ=1.10。
由于加工工況的復(fù)雜,使得聲發(fā)射信號(hào)的動(dòng)態(tài)范圍比較大,一般從微伏級(jí)到毫伏級(jí),因此聲發(fā)射傳感器均需前置放大器,這樣才能使得信號(hào)有效傳輸以利于后置處理。傳統(tǒng)的聲發(fā)射傳感器的放大倍數(shù)是固定的,而一般為了得到足夠的信號(hào)強(qiáng)度而首先滿足小信號(hào)的放大倍數(shù),這樣,信號(hào)稍大就會(huì)導(dǎo)致出現(xiàn)飽和現(xiàn)象。針對(duì)這一問題,研制了對(duì)數(shù)前置放大聲發(fā)射傳感器。依據(jù)式(2)的對(duì)數(shù)放大功能,可以壓縮聲發(fā)射輸入信號(hào)的動(dòng)態(tài)范圍,拓寬聲發(fā)射傳感器的監(jiān)測(cè)范圍。
U出=K1lg(K2.U入) (2)
式中U出—聲發(fā)射對(duì)數(shù)輸出信號(hào);
K1、K2—常數(shù)(一般稱為對(duì)數(shù)斜率);
U入—聲發(fā)射輸入信號(hào)。
4 監(jiān)控系統(tǒng)
主控模塊擔(dān)任監(jiān)控系統(tǒng)的主控任務(wù),并通過I/O模板管理鍵盤和液晶屏的顯示;聲發(fā)射調(diào)理模板完成前述的聲發(fā)射信號(hào)監(jiān)測(cè)處理任務(wù)并在出現(xiàn)異常狀態(tài)時(shí)報(bào)警,即向主控模板申請(qǐng)中斷;A/D、D/A模板完成對(duì)聲發(fā)射調(diào)理模板中聲發(fā)射包絡(luò)信號(hào)的采樣和把主控模板來的聲發(fā)射閾值送到聲發(fā)射調(diào)理模板進(jìn)行比較;并行通信模板完成監(jiān)控系統(tǒng)與機(jī)床控制系統(tǒng)之間通信任務(wù),即加工中心系統(tǒng)向監(jiān)控系統(tǒng)傳送各種工況參數(shù)和機(jī)床運(yùn)行狀態(tài)參數(shù),監(jiān)控系統(tǒng)向加工中心系統(tǒng)傳送刀具切削狀態(tài)信號(hào)。
本系統(tǒng)除手動(dòng)監(jiān)測(cè)方式外,還具有利用通信功能和一定范圍自動(dòng)浮動(dòng)閾值實(shí)現(xiàn)自動(dòng)監(jiān)測(cè)功能。系統(tǒng)具有模塊化,維修方便,使用可靠,抗干擾能力強(qiáng)的優(yōu)點(diǎn)。
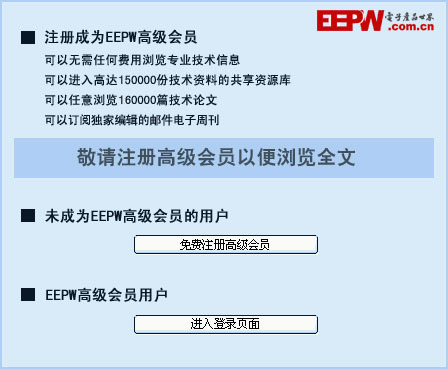
評(píng)論