基于S7-300 PLC的大型電弧爐控制系統(tǒng)
目前,在我國(guó)冶金行業(yè)中,大多數(shù)三相電弧冶煉電爐是靠人工凋整電弧電流進(jìn)行控制的。由于電弧爐的非線性、大滯后、強(qiáng)耦合、時(shí)變及隨機(jī)干擾較強(qiáng)等難點(diǎn),以及工人的經(jīng)驗(yàn)不同,冶煉的效果分散性很大,導(dǎo)致產(chǎn)品質(zhì)量下降,在冶煉的不同階段,控制效果很難一致,系統(tǒng)容易振蕩,增加電極消耗,嚴(yán)重時(shí)會(huì)引起斷電現(xiàn)象,不能保證三相電流的平衡輸入,產(chǎn)品質(zhì)量不穩(wěn)定,或者采用的控制器為BOOL型控制模式,輸出為通斷信號(hào),電極的升降速度為恒值,不能根據(jù)電弧電流的變化趨勢(shì)調(diào)整電極的升降速度,容易引起系統(tǒng)振蕩,使超調(diào)增大,調(diào)節(jié)過(guò)程加長(zhǎng),影響產(chǎn)品質(zhì)量,增加能耗,導(dǎo)致電極上下頻繁動(dòng)作,容易引起斷電現(xiàn)象,并縮短傳動(dòng)機(jī)構(gòu)的使用壽命。為了解決以上問(wèn)題,應(yīng)用自適應(yīng)控制理論,采用可編程控制器(PLC)為核心控制部件,實(shí)現(xiàn)了電弧爐電極升降的自動(dòng)準(zhǔn)確控制,有效地減少了電極短路、斷弧和振蕩現(xiàn)象。
本文引用地址:http://www.butianyuan.cn/article/265704.htm1 電弧爐電極自動(dòng)系統(tǒng)控制策略
1.1 電弧爐的冶煉過(guò)程工藝特點(diǎn)
電弧爐的冶煉過(guò)程為間歇式操作,每爐次主要分為引弧加料期和熔化期。前者的特點(diǎn)是電弧不穩(wěn)定,電流波動(dòng)極大,易發(fā)生斷弧、過(guò)電流跳閘和斷電極事故;后者的特點(diǎn)是弧溫較低,爐料比電阻較高,電極弧光埋在未熔化的爐料中,電流隨冶煉的進(jìn)行逐漸趨于平穩(wěn),如果控制的三相電極非平衡滿負(fù)荷送電,可能使?fàn)t料不能迅速熔化而延長(zhǎng)冶煉時(shí)問(wèn),增大功耗。
1.2 控制方案
依據(jù)經(jīng)典控制理論,只有建立了被控對(duì)象的數(shù)學(xué)模型,再按照系統(tǒng)工藝所要求的靜態(tài)指標(biāo)和動(dòng)態(tài)指標(biāo)設(shè)計(jì)校正環(huán)節(jié)的參數(shù),才能滿足工藝要求。但由于電弧爐具有多變量、非線性、大滯后、強(qiáng)耦合、數(shù)學(xué)模型參數(shù)的不確定性和系統(tǒng)工作點(diǎn)的劇烈變化等特點(diǎn),其實(shí)質(zhì)是一個(gè)多輸入、多輸出、非線性、強(qiáng)耦合的對(duì)象,顯然經(jīng)典控制對(duì)此無(wú)能為力,甚至用現(xiàn)代控制理論也不能精確地解決問(wèn)題,因?yàn)橄到y(tǒng)的特征所決定的數(shù)學(xué)模型難以建立,因此難以實(shí)現(xiàn)對(duì)被控量的精確控制。通過(guò)對(duì)電弧爐在冶煉過(guò)程中特點(diǎn)的了解,以及對(duì)被控對(duì)象特性的分析得知,電極調(diào)節(jié)系統(tǒng)是一個(gè)位置控制系統(tǒng),調(diào)節(jié)對(duì)象是弧長(zhǎng),但由于弧長(zhǎng)沒(méi)有合適的檢測(cè)設(shè)備,只能通過(guò)檢測(cè)電弧爐主電路的電弧電流間接地反映弧長(zhǎng)的大小,也就是通過(guò)控制電流來(lái)控制弧長(zhǎng)。
當(dāng)控制對(duì)象的特性或參數(shù)隨著環(huán)境的變化或運(yùn)行時(shí)間的加長(zhǎng)而大幅度變化時(shí),常規(guī)的反饋控制難以完成優(yōu)良的控制,而采用自適應(yīng)控制的控制方案比較合理。由電弧爐的功率特性曲線得知,不同的電弧電流對(duì)應(yīng)相同的電弧功率,當(dāng)弧流超過(guò)最有利的調(diào)節(jié)電流時(shí),輸入爐內(nèi)的功率并未因電流的增加而增大,反而線路的電耗增大,效率降低。在熔煉時(shí),將某一熔煉過(guò)程中最有利的調(diào)節(jié)電流作為電弧電流的額定值,再用自適應(yīng)控制來(lái)調(diào)整相關(guān)參數(shù)。
具體方法如下:當(dāng)系統(tǒng)開(kāi)始運(yùn)行時(shí),首先是點(diǎn)弧程序。其控制思路是:合高壓開(kāi)關(guān),冶煉開(kāi)始,三相電極自動(dòng)下降,在任一相電極接觸到導(dǎo)電爐料時(shí),該相電極自動(dòng)停止下降,直至另一電極起弧后第一相電極自動(dòng)起弧,這時(shí)系統(tǒng)自動(dòng)轉(zhuǎn)入熔煉程序,點(diǎn)弧程序結(jié)束。把電弧爐電流值的大小分為5個(gè)控制區(qū),如圖1所示。
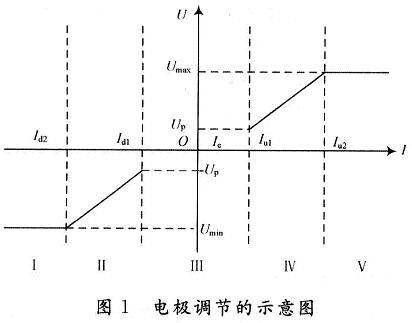
橫坐標(biāo)表示電弧電流值,縱坐標(biāo)表示PLC的輸出控制信號(hào)(-10~10 V),在工區(qū)電弧電流遠(yuǎn)遠(yuǎn)小于弧流額定值,PLC輸出的控制電壓為Umin,電極以最大的設(shè)定速度下降,該區(qū)也稱為下降飽和速度區(qū)。在Ⅱ區(qū)電弧電流小于弧流額定值,電極以速度線性減小下降,改變?cè)搮^(qū)的寬度就可以改變直線的斜率,也就調(diào)節(jié)了靈敏度,該區(qū)也稱為電極下降速度調(diào)節(jié)區(qū)。在Ⅲ區(qū)電弧電流等于或近似等于弧流額定值,PLC輸出的控制電壓為0,電極保持靜止不動(dòng),該區(qū)也稱為非調(diào)節(jié)區(qū)或死區(qū)。在Ⅳ區(qū)電弧電流大于弧流額定值,電極以速度線性增加上升,改變?cè)搮^(qū)的寬度就可以改變直線的斜率,也就調(diào)節(jié)了靈敏度,該區(qū)也稱為電極上升速度調(diào)節(jié)區(qū)。在V區(qū)電弧電流遠(yuǎn)遠(yuǎn)大于弧流額定值,PLC輸出的控制電壓為Umax,電極以最大的設(shè)定速度上升,該區(qū)也稱為上升飽和速度區(qū)。在非調(diào)節(jié)區(qū)與相鄰兩區(qū)的邊界點(diǎn),PLC輸出的控制電壓為±Up,Up為液壓伺服閥功率放大板的輸入門檻電壓值,0~Up的電壓不能使液壓閥有任何動(dòng)作。
在上述調(diào)節(jié)期間如果出現(xiàn)弧光竄動(dòng)、電流振蕩,甚至短路或斷弧時(shí),再按照一定的程序去調(diào)整死區(qū)寬度,調(diào)整靈敏度和飽和臨界值,這樣反復(fù)幾次,直到最佳參數(shù)為止。
對(duì)輸入PLC的信號(hào)進(jìn)行處理后,輸出可調(diào)的速度控制信號(hào)以控制電極動(dòng)作,使每相電極都能依據(jù)流過(guò)自身的電流而以相應(yīng)的速度上升、下降或停止,在保證系統(tǒng)穩(wěn)定性的同時(shí),又提高了系統(tǒng)的快速性,使電爐的冶煉電流始終處于最佳狀態(tài)。
2 工藝實(shí)踐
由該控制策略組建的自適應(yīng)控制系統(tǒng)已在某鋼廠調(diào)試通過(guò),并能可靠正常運(yùn)行。運(yùn)行結(jié)果表明,該系統(tǒng)控制精度高,可靠性高,動(dòng)態(tài)響應(yīng)速度快,弧流控制穩(wěn)定。提高了電極升降調(diào)節(jié)的快速性,可以保證電極平穩(wěn)調(diào)節(jié)。
2.1 系統(tǒng)硬件
電極升降自動(dòng)控制系統(tǒng)結(jié)構(gòu)框圖如圖2所示,圖中僅畫出A相電極控制框圖,B,C相和A相相同。
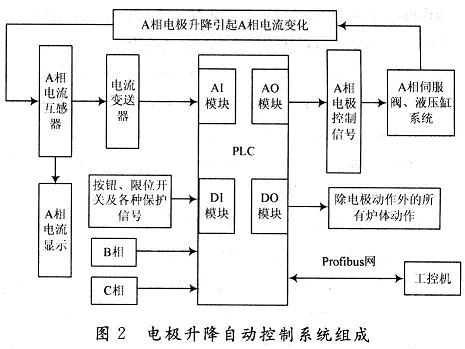
主要部分簡(jiǎn)介如下:
PLC選用西門子公司的S7-300 PLC作控制器。用于向上和上位機(jī)通訊,接受上位機(jī)的命令,并將工業(yè)現(xiàn)場(chǎng)的工況如實(shí)向上位機(jī)傳送。將弧流、弧壓數(shù)值、限位開(kāi)關(guān)、繼電器、電弧爐變壓器的各種保護(hù)電磁閥的狀態(tài)、斷路器的分合閘等信息送給工控機(jī)。向下接受各種模擬量和開(kāi)關(guān)量信號(hào)。同時(shí)控制三相伺服閥、液壓缸系統(tǒng)和各種現(xiàn)場(chǎng)設(shè)備。
上位機(jī)選用工業(yè)控制計(jì)算機(jī),通過(guò)工控軟件WINCC實(shí)現(xiàn)與下位機(jī)的對(duì)話,通過(guò)現(xiàn)場(chǎng)總線Profibus網(wǎng)對(duì)系統(tǒng)進(jìn)行實(shí)時(shí)監(jiān)控。
電流采集單元:由于電弧爐變壓器的二次側(cè)電流高達(dá)數(shù)萬(wàn)安培,因此將電流互感器安裝在一次側(cè)。電流采集單元的采集板將檢測(cè)到的相電流轉(zhuǎn)換成0~5 A的信號(hào),再轉(zhuǎn)換成4~20 mA的電流信號(hào),接到PLC的AI模塊中。同時(shí)將電壓互感器檢測(cè)到的信號(hào),一方面給顯示電路,一方面給PLC的AI模塊。
伺服閥、液壓缸系統(tǒng)是電極升降控制系統(tǒng)的執(zhí)行裝置,由電液伺服閥、液壓缸、背壓閥、換向閥等組成。該系統(tǒng)的液壓力為9 MPa。
2.2 軟件流程
系統(tǒng)用S7-300 PLC作為控制器,其軟件流程如圖3所示。
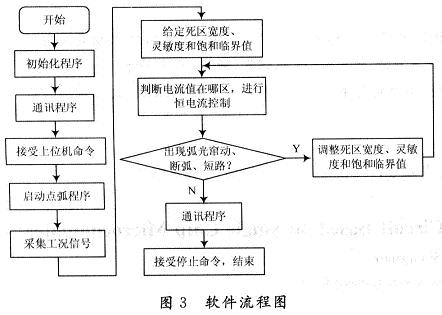
3 結(jié) 語(yǔ)
系統(tǒng)采用可靠性高,抗干擾能力強(qiáng)的S7-300 PLC作控制器。在此給出了采用靈敏度自適應(yīng)控制的控制方案,對(duì)電弧爐的電極進(jìn)行自動(dòng)控制,克服了外界環(huán)境對(duì)電極控制的影響。該系統(tǒng)已在某煉鋼廠可靠運(yùn)行。達(dá)到了降低電爐電耗,減輕工人勞動(dòng)強(qiáng)度,提高產(chǎn)品質(zhì)量的目的。
互感器相關(guān)文章:互感器原理
西門子plc相關(guān)文章:西門子plc視頻教程
斷路器相關(guān)文章:斷路器原理
高壓真空斷路器相關(guān)文章:高壓真空斷路器原理 漏電斷路器相關(guān)文章:漏電斷路器原理
評(píng)論