PCB組裝設(shè)計的14個技巧
設(shè)計與PCB組裝記住是最重要和最常被誤解的元素之一。本系列致力于幫助您成為一名設(shè)計專家——PCB 設(shè)計在第一次嘗試時就得到優(yōu)化,確保順利快速的 PCB 生產(chǎn)過程。在為裝配進行設(shè)計時,請遵循以下提示。
通過本文的課程,我們將涵蓋:
目錄
1、什么是裝配設(shè)計 (DFA)?
2、成為PCB組裝大師
2.1.注意零件間距。
2.2.在設(shè)計階段選擇組件。
2.3.將非無鉛元件與無鉛元件分開。
2.4.均勻放置大型組件。
2.5.避免混合技術(shù)。
2.6.選擇合適的包裝尺寸。
2.7.尋找提前期較長的組件。
2.8.保持設(shè)計時的 BOM 是最新的。
2.9.仔細檢查您的封裝。
2.10.確保所有有方向性的都有指示。
2.11.必須填充焊盤上的過孔。
2.12.一個焊盤一個連接。
2.13.簡化 CAM 設(shè)置。
2.14.解決您的組件交付問題。
2.15.檢查這些額外的 PCB 組裝技巧。
1、什么是裝配設(shè)計 (DFA)?在進一步討論之前,讓我們討論一下PCB組裝包含。在提交并批準 PCB 設(shè)計后——無論是柔性、高密度互連 (HDI) 還是其他——它就被制造出來了。完成后,裸板將需要與其他組件組裝在一起,包括處理器和記憶.
足夠簡單。經(jīng)常出現(xiàn)的問題——至少在那些還不是 PCB 大師的人中——是最初的 PCB 設(shè)計沒有完全考慮到組裝。相反,他們只關(guān)注電路板本身,而沒有更廣泛的上下文來說明電路板將如何在產(chǎn)品或應(yīng)用程序中使用。
忽視 PCB 組裝會導致嚴重的并發(fā)癥。孤立地看,PCB 設(shè)計似乎是完全可以接受的,但某些設(shè)計決策可能會使以后的組裝變得困難。例如,組件可能彼此靠得太近,這可能導致產(chǎn)品無法正常運行,或?qū)е滦阅軉栴}。我們將在本文后面深入討論這一點。
然后還有組件可用性的問題。為了使 PCB 組裝過程順利進行,從而使整個 PCB 生產(chǎn)有效地進行,組裝供應(yīng)商需要在電路板到達后立即準備好所需的組件。如果它們不可用,則整個過程將被延遲,從而削弱 PCB 生產(chǎn)快速周轉(zhuǎn)方法的價值。在此處查看獲取輕松電路板報價的提示,請求 PCB 報價時最缺少的信息。
2、成為PCB組裝大師如果您在設(shè)計時沒有考慮 PCB 組裝,這些只是會出現(xiàn)的一些問題。問題是,PCB高手如何避免犯這些錯誤呢?以下是一些關(guān)鍵提示。
2.1.注意零件到零件的間距。尚未成為 PCB 大師的設(shè)計師提出的常見問題之一是關(guān)于組件到組件的間距。將一個組件放置得離另一個組件太近會產(chǎn)生各種問題,這些問題可能需要重新設(shè)計和重新制造,從而導致時間和金錢的損失。
PCB 母版使用多種技術(shù)來避免組裝過程中的部件與部件之間的間距問題。他們以這樣一種方式設(shè)計他們的足跡,即在組件邊界之間總是有足夠的間隙。這減輕了由于組件在放置期間過于靠近而可能產(chǎn)生的任何潛在問題。
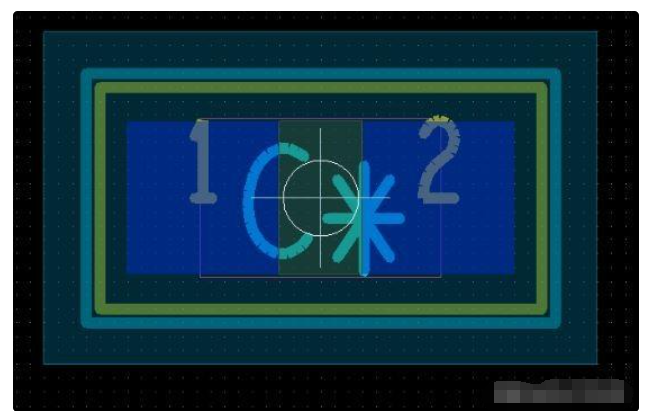
將綁定的形狀放在絲綢和裝配線周圍。
設(shè)計人員必須小心地放置組件,以便放置綁定的組件形狀不會相互重疊。在示例一中,您可以看到根據(jù)位置綁定形狀放置組件將自動使它們相距 50 密耳。如果電路板沒有足夠的空間,PCB Masters 可以忽略位置綁定的形狀并將組件移近彼此,同時牢記最小間距規(guī)則。
確保在您的 PCB 設(shè)計軟件中建立了組件規(guī)則、要求和接近度規(guī)定。PCB 母版針對各種零件類型制定了特定的組件到組件間距指南。例如,電容和電阻等分立元件之間的最小間距應(yīng)始終至少為 10 密耳,30 密耳為首選間距。這個簡單的操作將有助于避免許多鄰近問題。否則,這些問題可能會導致組裝延遲或其他并發(fā)癥。有關(guān)其他間距規(guī)則,請參閱表 1.1。
表 1.1:組件到組件的間距
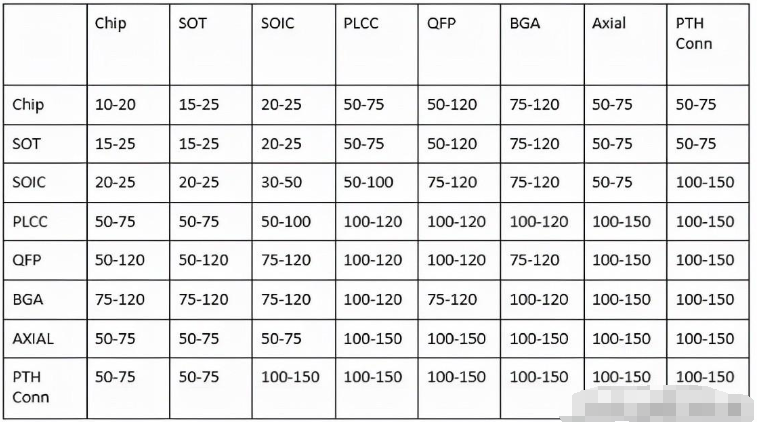
根據(jù)設(shè)計約束和裝配供應(yīng)商的能力,上述值可能會發(fā)生變化。
PCB 大師在設(shè)計過程的早期選擇組件,意識到這是確保實際設(shè)計和正在組裝的組件之間不存在沖突的最佳方式。如果您從一開始就考慮元件尺寸,則元件空間和尺寸不再是問題,PCB 組裝過程可以毫無障礙地進行。這也引出了下一個技巧。
PCB 設(shè)計人員應(yīng)該與電路設(shè)計人員和工程師交談,看看是否可以減小組件尺寸,從而在板上創(chuàng)造額外的空間。畢竟,更小的部件意味著電路板上的占用空間更小。
要了解有關(guān) PCB 設(shè)計基礎(chǔ)知識的更多信息,請閱讀,掌握PCB設(shè)計基礎(chǔ)的藝術(shù).
2.3. 將非無鉛元件與無鉛元件分開。切勿將無鉛組件與未指定用于無鉛組裝的組件混合。如果任何組件需要無鉛組裝,并且無法替代傳統(tǒng)的含鉛焊料,則整個電路板必須無鉛組裝,并且所有組件都必須符合無鉛組裝的要求。
有時,特定設(shè)備唯一可用的封裝是無鉛BGA。然而,根據(jù)政府要求,用于軍事項目的電路板通常必須使用傳統(tǒng)的含鉛焊料進行組裝。設(shè)計師必須獲得客戶的豁免,以允許無鉛組裝;修改設(shè)計,以使用可在包裝中使用的設(shè)備,用于使用傳統(tǒng)鉛焊料進行組裝;或者讓BGA重新填充含鉛焊料(這是一個昂貴的過程,可能會損壞零件)。

拼板的板邊干擾了在該邊緣上延伸的連接器的組裝。當電路板制造和組裝沒有緊密協(xié)調(diào)時,就會出現(xiàn)此類問題。
在布局期間盡可能均勻地分布整個電路板上的大型元件,以在回流焊期間實現(xiàn)最佳的熱分布。確保裝配承包商為每個裝配工作所獨有的回流焊爐量身定制熱配置文件。
2.5. 避免混合技術(shù)。盡可能避免混合技術(shù)。例如,單個通孔的回報不會超過花費的額外時間和金錢。使用多個通孔或不使用會更有效。如果您確實使用通孔技術(shù),將所有通孔放置在電路板的一側(cè)將減少制造時間。
2.6. 選擇合適的封裝尺寸。電氣工程師和 PCB 設(shè)計人員之間的溝通應(yīng)該在布局的早期階段開始。設(shè)計人員應(yīng)審查 BOM 并仔細檢查設(shè)計中使用的零件。如果板上有空間并且當前設(shè)計使用了不必要的小組件,設(shè)計人員可能會推薦更大的組件。這將有助于避免組裝過程中的多種工藝。例如,盡可能使用 0402 尺寸的電容器/電阻器而不是 0201 。
如果 0805 能夠滿足所有必要的要求,PCB Master 會選擇 0805 電容器而不是 1206 電容器。這將釋放板上的大量空間。

與大型組件相比,較小尺寸的組件更容易獲得。
它們也由不同的供應(yīng)商制造。選擇這些組件將避免組裝過程中的延誤。它還為電氣工程師或設(shè)計師提供了選擇替代零件的選項,而無需更改原理圖或布局,及時解決沒有庫存的組件。
最后,在 PCB 設(shè)計階段選擇合適的封裝尺寸很重要。PCB Master 僅在有充分理由時才選擇較小的封裝;否則,傾向于更大的選擇。在太多情況下,電氣工程師會選擇不必要的小組件封裝。這可能會在組裝良率方面產(chǎn)生問題,因為修補和返工較小的組件更加困難。根據(jù)所需的返工量,完全重建電路板并移除和焊接新組件可能更具成本效益。
在確認理想的封裝尺寸后,您可以開始選擇相同密度類別的組件。
2.7. 尋找交期短的組件。如上所述,組件可用性可能會導致顯著延遲。然而,PCB 大師通過在開始設(shè)計之前檢查所有組件的可用性來避免這個問題。如果有需要較長交貨期的零件,可以提前訂購并委托給PCB組裝供應(yīng)商。組裝供應(yīng)商還可以處理更廣泛可用零件的采購,因此當您的電路板準備好組裝時,每個組件都將準備就緒并等待。
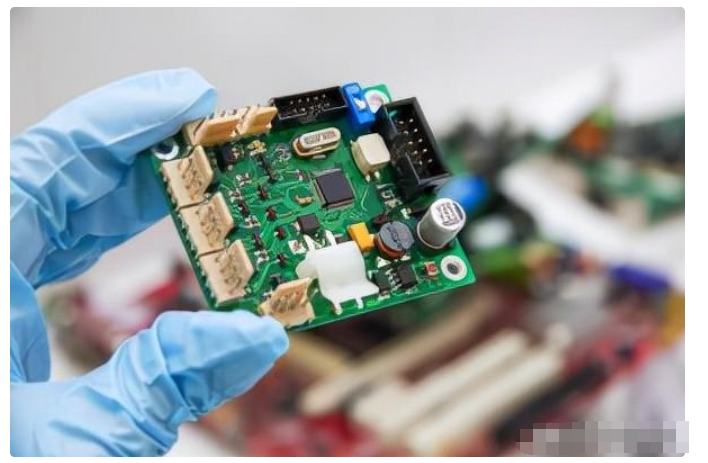
在設(shè)計的早期階段檢查組件的可用性。
BOM 是設(shè)計和裝配的關(guān)鍵方面。如果您的 BOM 中有任何問題,裝配廠將暫停項目,直到問題與工程師一起解決。確保您的 BOM 更新的一種方法是在您的設(shè)計發(fā)生更改時隨時查看您的 BOM。當您在布局過程中向原理圖添加新組件時,請確保您還使用正確的部件號、描述和組件值更新了 BOM。在設(shè)計過程中,工程師可能會因提前期、尺寸或可用性而更改組件,而忘記使用新零件號更新 BOM。這可能會導致各種組裝問題并導致延遲。
格式化每個材料清單根據(jù)以下示例精確識別每塊板上要組裝的所有組件。格式正確的 BOM 的列指示:
完整的制造商部件號
制造商名稱
項目編號
每板數(shù)量
參考指示符,以逗號分隔
完整的零件描述
它還可能包括:
經(jīng)銷商名稱
分銷商的零件號

每個項目 BOM保持相同的格式
元件封裝是布局設(shè)計的另一個主要方面。PCB Master 將確保按照數(shù)據(jù)表中推薦的焊盤圖案準確創(chuàng)建其封裝。正確使用數(shù)據(jù)表中的編號鍵來識別正確的部件及其焊盤圖案非常重要。錯誤地閱讀數(shù)據(jù)表將導致不正確的占位面積,這可能需要對電路板進行完整的重新設(shè)計和重新制造。
下圖顯示了編號鍵和各種類型的封裝的示例。

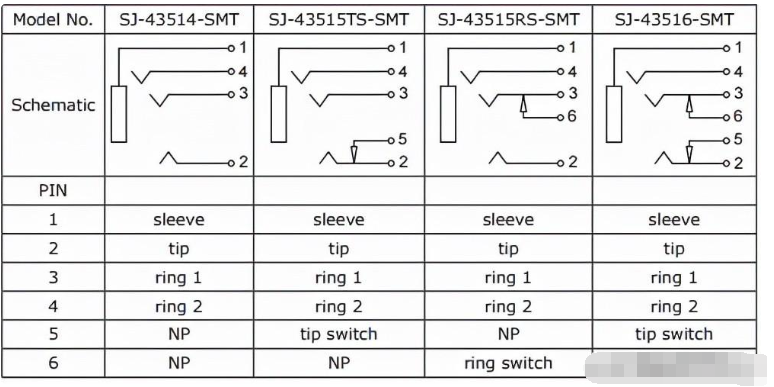
請注意每個型號的型號和相關(guān)引腳。
2.10. 確保所有帶方向的都有標識。組裝中的主要顯示停止器缺少絲印上的引腳 1 指示器或組件極性/方向指示器。我的工廠收到的組裝訂單中,有近 75% 無法識別每個 IC 的引腳 1 的位置,或者他們歪曲或忽略指示某些電容器、二極管或 LED 的極性。
避免裝配問題的最佳方法:甚至在設(shè)計開始之前與您的制造商協(xié)商。
遵守二極管(包括LED)極性標記的約定:在陰極端的絲印層上打一個K?;蛘?,以正確的方向使用二極管的電氣符號來指導組裝。切勿根據(jù)陽極焊盤指示二極管極性。使用 K 來指定陰極或?qū)⒍O管符號排列在正確的位置。不要替換任何其他標記,否則您的承包商會誤解您的意圖。
要定位鉭電容器,請在絲印上用加號標記正極。請記住,如果以交換極性安裝,鉭電容器可能會點燃。除非對原理圖進行逆向工程,否則承包商無法確定零件極性,除非它清楚地顯示出來。絲印不得干擾焊盤,并且不得在任何組件的主體下方印刷符號。
2.11. 必須填充焊盤上的過孔。除非他們住在熱墊,過孔焊盤必須填寫。將安裝 BGA 的焊盤矩陣可能包括通孔和盲孔,但所有這些都必須填充和平面化,否則會損害焊點。在下面的散熱墊中加入過孔QFN以幫助焊料流過導電平面。這些過孔確保了散熱焊盤的安全焊點,并防止在組裝過程中焊料漂浮在封裝上,這可能會妨礙在 QFN 觸點處形成良好的焊點。裝配車間可以通過在焊盤上方的焊膏模板中添加窗玻璃形狀的開口來補償散熱焊盤中缺少通孔的情況,以緩解焊料池和放氣在組裝期間,但修復(fù)效果不如存在過孔的情況下。
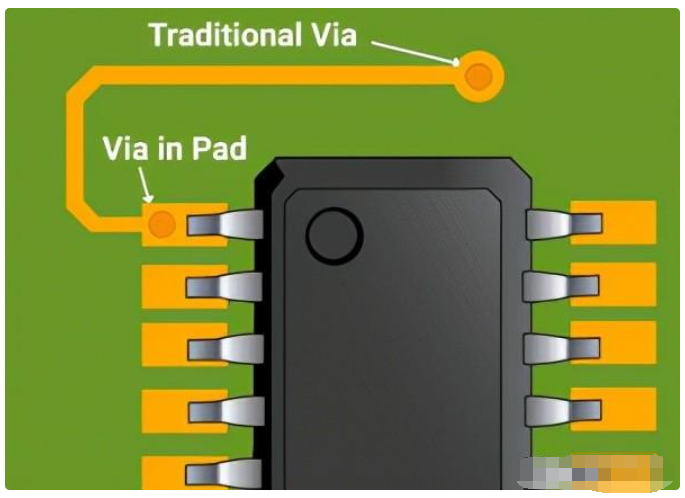
焊盤上的過孔圖片
每個組件的每個連接都必須有自己的獨立焊盤。每個墊的尺寸必須與其配合件相稱。如果兩個組件共享一個焊盤——比如說,一個電阻器和一個電容器——在組裝過程中它們都不能正確對齊。如果一個焊盤遠大于其對組件的配對,則組件墓碑可能是由于焊料沉積的不平衡造成的。
如果澆注或平面將是一個接觸點,則必須有一個適當大小的掩碼定義的墊。如果器件包括用于連接的非阻焊層定義的焊盤以及阻焊層——定義的焊盤是松散間距上的 BGA 矩陣,例如,其中一些相鄰的外球與接地澆注共用——在設(shè)計說明中規(guī)定電路板制造商不得為那些阻焊層定義的焊盤編輯阻焊層孔徑。
要了解焊盤設(shè)計,請閱讀PCB設(shè)計開發(fā)中的焊盤是什么?
2.13. 簡化 CAM 設(shè)置。不用說,在制造電路板之前發(fā)現(xiàn)可能阻礙組裝的問題要好得多。如果電路板將由同一設(shè)施制造和組裝(從而協(xié)調(diào)操作),請驗證是否提供設(shè)計數(shù)據(jù)ODB++ 格式以加快識別潛在的制造問題并簡化 CAM 設(shè)置。在 ODB++ 中輸出設(shè)計以統(tǒng)一結(jié)構(gòu)捕獲制造、裝配和測試數(shù)據(jù),該結(jié)構(gòu)支持自動分析并避免在 CAM 階段進行耗時的數(shù)據(jù)轉(zhuǎn)換。實際上,所有主要的 EDA 平臺都可以以 ODB++ 格式輸出設(shè)計數(shù)據(jù)。
2.14. 解決您的組件交付問題。從技術(shù)上講,第 10 條提示不涉及設(shè)計,而是將組件交付給承包商。如果組裝將在寄售的基礎(chǔ)上進行——部分或全部組件將由組裝客戶提供,而不是由組裝商采購——部件必須以與 BOM 匹配的精心組織的套件提供。所有 SMT 組件都必須以卷軸或至少 6 英寸長的連續(xù)膠帶或管或托盤的形式提供。
BOM 上列出的每個零件號都需要額外的組件,以彌補裝配過程中的磨損。例如,裝配車間可能需要比 BOM 要求的最少 100 或 20% 的 0201 1k 歐姆電阻器。BOM 上每個行項目的零件必須在與其他零件分開的清楚標記的袋子中發(fā)送。所有 IC 都必須在包含干燥劑的原始、未開封的保護性包裝中運輸,否則它們必須在組裝前烘烤 8 小時左右以去除水分,這可能會使組裝推遲一天。
換句話說,8 個 1005 尺寸的 12pF 電容器的 8 個條帶不滿足該部件 64 個的 BOM 要求。條帶太短,無法裝載取放供料器,在最好的情況下,并非所有零件都會卷到板上。在發(fā)貨前使用我們的配套指南檢查并仔細檢查您的組件。
最后,讓我推薦避免裝配問題的最佳方法:在設(shè)計開始之前與您的制造商協(xié)商。
2.15. 檢查這些額外的 PCB 組裝技巧。在設(shè)計階段要記住的其他裝配細節(jié)包括加熱和清洗。確保您知道您的組件的最高熱量水平是多少,它們是否可以清洗,以及它需要的組裝類型。如果是手工焊接,電路板設(shè)計必須包括用于焊接工具的空間。
確保您的電容器都面向同一方向。這節(jié)省了取放機元件放置期間的時間。
注意散發(fā)熱量的組件。必須仔細檢查這些組件周圍的空間。確保熱量不會對任何組件或組件周圍的走線產(chǎn)生負面影響。
*博客內(nèi)容為網(wǎng)友個人發(fā)布,僅代表博主個人觀點,如有侵權(quán)請聯(lián)系工作人員刪除。