參數(shù)曲面的快速實(shí)時(shí)插補(bǔ)
一、數(shù)控系統(tǒng)的離線插補(bǔ)
本文引用地址:http://www.butianyuan.cn/article/161967.htm在數(shù)控系統(tǒng)中,傳統(tǒng)的離線插補(bǔ)方法須先通過幾何造型系統(tǒng)進(jìn)行造型,在此基礎(chǔ)上,通過人工交互方式輸入有關(guān)的加工工藝信息,再通過離線方式生成相關(guān)刀位文件,之后通過后處理生成具體機(jī)床的代碼指令序列。從中可以看出,這種離線方式不僅環(huán)節(jié)多,需消耗大量的人工和機(jī)時(shí),占用較多的軟硬件資源,而且由于刀具路徑規(guī)劃與軌跡相分離,難以實(shí)現(xiàn)刀具尺寸的三維實(shí)時(shí)準(zhǔn)確補(bǔ)償,使加工和編程需多次進(jìn)行,延長(zhǎng)了加工時(shí)間。同時(shí),該過程需對(duì)大量數(shù)據(jù)進(jìn)行編碼、解碼、傳送、存儲(chǔ)和處理,大大增加了出錯(cuò)的概率,對(duì)數(shù)控的可靠性造成不利的影響。
為了避免離線編程的固有不足,人們提出了實(shí)時(shí)插補(bǔ)的技術(shù),即數(shù)控系統(tǒng)根據(jù)被加工曲面的有關(guān)信息,實(shí)時(shí)生成無干涉的刀位軌跡和產(chǎn)生刀具運(yùn)動(dòng)的控制指令,由此實(shí)現(xiàn)對(duì)加工過程的控制。但該方法對(duì)插補(bǔ)技術(shù)要求較高,即要求插補(bǔ)算法的效率高,因?yàn)橐獙?shí)施實(shí)時(shí)插補(bǔ),插補(bǔ)系統(tǒng)必須在插補(bǔ)周期內(nèi)計(jì)算出下一步插補(bǔ)點(diǎn)的坐標(biāo),并進(jìn)行干涉等相關(guān)技術(shù)的處理。因此,目前很多CNC 機(jī)床只能對(duì)直線和圓弧進(jìn)行直接插補(bǔ),還無法對(duì)曲面進(jìn)行實(shí)時(shí)插補(bǔ)。為了改善上述狀況,我們仔細(xì)研究了數(shù)控加工和曲面實(shí)時(shí)插補(bǔ)的相關(guān)技術(shù),提出了一種參數(shù)曲面的實(shí)時(shí)插補(bǔ)算法,該算法思路獨(dú)特,大大縮短了參數(shù)曲面實(shí)時(shí)插補(bǔ)的時(shí)間,顯著提高了實(shí)時(shí)插補(bǔ)效率,從而使自由曲面實(shí)時(shí)插補(bǔ)成為可能。
二、插補(bǔ)的基本原理
當(dāng)前數(shù)控加工系統(tǒng)的插補(bǔ)方法主要分為兩大類:一類為脈沖增量插補(bǔ),即行程標(biāo)量插補(bǔ):另一類為數(shù)據(jù)采樣插補(bǔ),即時(shí)間標(biāo)量插補(bǔ)。脈沖增量插補(bǔ)是用步進(jìn)器在每一個(gè)脈沖時(shí)間內(nèi)的進(jìn)距作為插補(bǔ)單位進(jìn)行插補(bǔ),此方法主要常見于開環(huán)數(shù)控系統(tǒng)中,用于直線和圓弧的插補(bǔ),插補(bǔ)速度一般較慢。而數(shù)據(jù)采樣插補(bǔ)是以刀具在一個(gè)插補(bǔ)周期內(nèi)所走的距離進(jìn)行插補(bǔ),該方法可用于較為復(fù)雜的曲線的插補(bǔ),且可實(shí)現(xiàn)快速插補(bǔ)??紤]到脈沖增量插補(bǔ)一些固有的不足,本文采用數(shù)據(jù)采樣方法進(jìn)行插補(bǔ)。該方法的原理是先根據(jù)進(jìn)給速度和插補(bǔ)周期算出在一個(gè)插補(bǔ)周期內(nèi)刀具在合成速度方向上的進(jìn)給量,之后在實(shí)際插補(bǔ)時(shí)根據(jù)實(shí)時(shí)測(cè)得的值和理論值的差通過伺服機(jī)構(gòu)控制各個(gè)運(yùn)動(dòng)軸進(jìn)行插補(bǔ)。
三、參數(shù)曲面的實(shí)時(shí)插補(bǔ)
本文提出的曲面實(shí)時(shí)插補(bǔ)采用截平面法。該方法分成3部分。首先對(duì)被加工曲面進(jìn)行離散化,然后用一組平行面對(duì)其進(jìn)行截交,求出截交線,并求出初始插補(bǔ)點(diǎn),最后對(duì)這些初始插補(bǔ)點(diǎn)進(jìn)行干涉處理生成刀位軌
參數(shù)曲面的離散化
對(duì)于參數(shù)曲面的離散化,目前研究比較多。本文采用四叉樹對(duì)曲面進(jìn)行自適應(yīng)三角形離散化,即首先根據(jù)曲面要求的加工精度計(jì)算出離散時(shí)允許的離散精度,再根據(jù)此離散精度對(duì)曲面進(jìn)行遞歸細(xì)分,當(dāng)其中的子曲面片在遞歸細(xì)分過程中被判定在離散精度允許精度內(nèi)為局部平坦時(shí)則停止對(duì)其進(jìn)一步細(xì)分,這樣一直進(jìn)行到所有的子曲面片都為局部平坦為止。之后,通過取局部平坦的子曲面片四個(gè)角點(diǎn)的中心將每個(gè)子曲面片轉(zhuǎn)化為四個(gè)三角形片。這樣,經(jīng)過離散化后,該參數(shù)曲面將有一系列三角平面片代替。
平面與曲面進(jìn)行截交生成初始插補(bǔ)點(diǎn)
目前,刀軌生成形式有等參數(shù)線法、截平面法和環(huán)切法。其中截平面法刀軌生成質(zhì)量較高,故本文采用截平面法。截平面法就是用一組一般取垂直于XY 面的平行平面去截被加工的曲面并用它們的交線進(jìn)行相關(guān)的處理以生成刀位軌跡的方法。
由于加工曲面通過前步的離散化處理已有一系列簡(jiǎn)單的三角平面片組成,故對(duì)平面和曲面的交線求解比較單,只需求該平面和相關(guān)的三角平面片的交線即可。不過,此處必須說明的是,前步的離散化處理由于相鄰的子曲面片細(xì)分層次不一樣可能出現(xiàn)裂縫和折疊現(xiàn)象,見附圖。當(dāng)然這種現(xiàn)象可通過一定的手段進(jìn)行消除,但這將大大降低離散的效率而不為本文所采用。本文將該問題在此處只需稍作處理即可。當(dāng)平面與裂縫處的三角平面片截交時(shí)會(huì)與裂縫之間產(chǎn)生交線,比如附圖中的線段AB,而實(shí)際上AB兩點(diǎn)應(yīng)為曲面的同一點(diǎn),只是由于離散方法的不完善而產(chǎn)生。為了消除這一現(xiàn)象,本文采用的方法為在這種情況下,取A、B兩點(diǎn)的中點(diǎn)為C為平面與裂縫處子曲面片的邊界的交點(diǎn)。
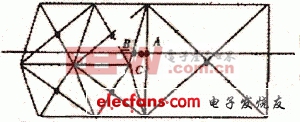
附圖 離散化過程中出現(xiàn)的裂紋
評(píng)論